Critically analyse the eight elements of total quality management and determine which you believe are present in the case study.
Critically analyse the eight elements of total quality management and determine which you believe are present in the case study.
Chapter1: Taking Risks And Making Profits Within The Dynamic Business Environment
Section: Chapter Questions
Problem 1CE
Related questions
Question
Critically analyse the eight elements of total quality management and determine which you believe are present in the case study.

Transcribed Image Text:So far, Nissan has invested over £2.1 billion in the Sunderland site, taking its production capacity to
500,000 vehicles per year. Car assembly is a complex operation with many components requiring
skilled assembly. Management is particularly keen to monitor the total machine hours and total
labour hours that each vehicle requires.
In pursuit of high output at a low average cost, car manufacturing typically uses a continuous flow
production method, where sub-assemblies are brought together in a final assembly area. This is the
most cost-effective and efficient method of production and the speed of the final assembly line can
be adjusted to match consumer demand. If demand picks up, the production line can be accelerated,
within predefined limits.
At NMUK, the production flow draws on three main production shops, as well as support areas. The
three main shops are:
• body assembly
painting
final assembly
One key decision with a car plant is where to locate it. For its UK factory, Nissan chose in 1984 a
300hectare former airfield near Sunderland. Sunderland's attractions included:
a) Skilled labour force
Manufacturing has a long tradition in the area. A decline in other local manufacturing meant that
skilled labour was readily available.
b) Communications
Sunderland has good road and rail links to all major UK areas. This makes it relatively easy to bring in
supplies from 105 separate UK component and sub-assembly suppliers, and also to distribute
completed vehicles. A nearby deepwater port (Port of Tyne) gives ready access to export markets and
for the import of vehicles to the UK.
c) Government support
The government provided financial and other incentives to manufacturers who set up in an area
where employment opportunities had reduced sharply and new jobs were needed.
4/5

Transcribed Image Text:Nissan is famously associated with 'Kaizen' or continuous quality improvement. Nissan states: 'We will
not be restricted by the existing way of doing things. We will continuously seek improvements in all
our actions.
Kaizen can be applied everywhere, any time, any place. It can involve the smallest change in everyday
working practice as well as a major change in production technology. Typically these improvements
are initiated by teams of employees sitting down together and sharing ideas for improvements. Small
steady changes are maintained to make sure that they actually work. No improvement is too small.
Everyone at Nissan is responsible for thinking about the current way of doing a job and finding a better
way of doing things.
Kaizen improvements can save:
Money, time, materials, labour effort as well as improving quality, safety, job satisfaction, and
productivity.
Productivity levels at Nissan's plant in Sunderland, and the quality of final production there, have not
happened by chance or good fortune. They stem from an all-embracing approach to a production
process, designed to bring out the best in both people and machines. It continues to be conspicuously
successful.
It is vital to train people to work in such a hi-tech industry with such sophisticated quality systems.
NMUK's training department conducts a training needs analysis to assess individual employees' needs
and to organise training programmes.
The department concentrates on five main areas:
1. technical development
2. people development
3. understanding processes
4. computer skills and graduate training
5. trainee development
Total Quality Management (TQM) is a key feature of Nissan's way of working. TQM involves making
customer satisfaction a top priority. Given this goal, everything the organisation and its people do is
focused on creating high quality.
To achieve this, Nissan has to:
• understand customer requirements
consider the processes involved in providing quality, not just the end result
prioritise and standardise tasks to deliver quality
educate all employees to work in this way.
Nissan Motor Company Ltd, usually shortened to Nissan is a Japanese multinational automobile
manufacturer headquartered in Nishi-Ku, Yokohama, Japan.
Nissan Motor sells its cars under the Nissan, Infiniti, Datsun and NISMO brands.
With a just-in-time approach, specific vehicles and their components are produced just-in-time to
meet the demand for them. Sub-assemblies move into the final assembly plant just as final assemblers
are ready to work on them, components arrive just in time to be installed, and so on. In this way, the
amount of cash tied up in stocks and in work-in-progress is kept to a minimum, as is the amount of
space devoted to costly warehousing rather than to revenue-generating production. Nissan's just-in-
time process depends not on human frailty but on machine precision.
The emphasis placed on 'going for quality' means that each employee is responsible both for their
own work and the standards of their co-workers. By ensuring management recognises that individuals
have this control results in everyone taking the culture onboard.
Nissan expects and requires its employees to become multi-skilled decision-makers. Most employees
also want that for themselves.
Reaching that goal involves:
.
.
.
.
.
training employees to develop their skills
encouraging them to make decisions
organising employees into participative teams
developing open-channel, multi-directional communication systems
placing quality at the heart of flow production
flexible working practices
providing the employee variety within his/her role
3/5
Expert Solution

This question has been solved!
Explore an expertly crafted, step-by-step solution for a thorough understanding of key concepts.
Step by step
Solved in 2 steps

Recommended textbooks for you
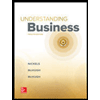
Understanding Business
Management
ISBN:
9781259929434
Author:
William Nickels
Publisher:
McGraw-Hill Education
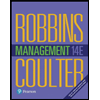
Management (14th Edition)
Management
ISBN:
9780134527604
Author:
Stephen P. Robbins, Mary A. Coulter
Publisher:
PEARSON
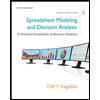
Spreadsheet Modeling & Decision Analysis: A Pract…
Management
ISBN:
9781305947412
Author:
Cliff Ragsdale
Publisher:
Cengage Learning
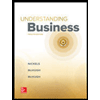
Understanding Business
Management
ISBN:
9781259929434
Author:
William Nickels
Publisher:
McGraw-Hill Education
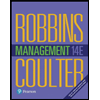
Management (14th Edition)
Management
ISBN:
9780134527604
Author:
Stephen P. Robbins, Mary A. Coulter
Publisher:
PEARSON
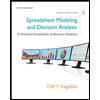
Spreadsheet Modeling & Decision Analysis: A Pract…
Management
ISBN:
9781305947412
Author:
Cliff Ragsdale
Publisher:
Cengage Learning
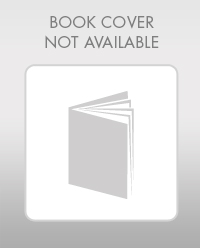
Management Information Systems: Managing The Digi…
Management
ISBN:
9780135191798
Author:
Kenneth C. Laudon, Jane P. Laudon
Publisher:
PEARSON
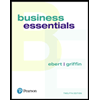
Business Essentials (12th Edition) (What's New in…
Management
ISBN:
9780134728391
Author:
Ronald J. Ebert, Ricky W. Griffin
Publisher:
PEARSON
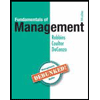
Fundamentals of Management (10th Edition)
Management
ISBN:
9780134237473
Author:
Stephen P. Robbins, Mary A. Coulter, David A. De Cenzo
Publisher:
PEARSON