E4-23A Use ABC to allocate manufacturing overhead (Learning Objective 2) Several years after reengineering its production process, Biltmore Corporation hired a new controller, Rachael Johnson. She developed an ABC system very similar to the one used by Biltmore’s chief rival, Westriver. Part of the reason Johnson developed the ABC system was because Biltmore’s profits had been declining even though the company had shifted its product mix toward the product that had appeared most profitable under the old system. Before adopting the new ABC system, Biltmore had used a plantwide overhead rate based on direct labor hours that was developed years ago. For the upcoming year, Biltmore’s budgeted ABC manufacturing overhead allocation rates are as follows: Activity Allocation Base Activity Cost Allocation Rate Materials handling # of parts $3.84 per part Machine setup # of setups $330.00 per setup Insertion of parts # of parts $30.00 per part Finishing Finishing DL hrs $54.00 per hour The number of parts is now a feasible allocation base because Biltmore recently installed a plantwide computer system. Biltmore produces two wheel models: Standard and Deluxe. Budgeted data for the upcoming year are as follows: Standard Deluxe Parts per wheel……………………. 6.0 8.0 Setups per 1,000 wheels…………… 20.0 20.0 Finishing DL hrs per wheel………... 1.2 3.3 Total DL hrs per wheel…………….. 2.0 3.3 The company’s managers expect to produce 1,000 units of each model during the year. Requirements 1. Compute the total budgeted manufacturing overhead cost for the upcoming year 2. Compute the manufacturing overhead cost per wheel of each model using ABC. 3. Compute Biltmore’s traditional plantwide overhead rate. Use this rate to determine the manufacturing overhead cost per wheel under the traditional system.
E4-23A Use ABC to allocate manufacturing
Several years after reengineering its production process, Biltmore Corporation hired a new controller, Rachael Johnson. She developed an ABC system very similar to the one used by Biltmore’s chief rival, Westriver. Part of the reason Johnson developed the ABC system was because Biltmore’s profits had been declining even though the company had shifted its product mix toward the product that had appeared most profitable under the old system. Before adopting the new ABC system, Biltmore had used a plantwide overhead rate based on direct labor hours that was developed years ago.
For the upcoming year, Biltmore’s budgeted ABC manufacturing overhead allocation rates are as follows:
Activity Allocation Base Activity Cost Allocation Rate
Materials handling # of parts $3.84 per part
Machine setup # of setups $330.00 per setup
Insertion of parts # of parts $30.00 per part
Finishing Finishing DL hrs $54.00 per hour
The number of parts is now a feasible allocation base because Biltmore recently installed a plantwide computer system. Biltmore produces two wheel models: Standard and Deluxe. Budgeted data for the upcoming year are as follows:
Standard Deluxe
Parts per wheel……………………. 6.0 8.0
Setups per 1,000 wheels…………… 20.0 20.0
Finishing DL hrs per wheel………... 1.2 3.3
Total DL hrs per wheel…………….. 2.0 3.3
The company’s managers expect to produce 1,000 units of each model during the year.
Requirements
1. Compute the total budgeted
2. Compute the manufacturing overhead cost per wheel of each model using ABC.
3. Compute Biltmore’s traditional plantwide overhead rate. Use this rate to determine the manufacturing overhead cost per wheel under the traditional system.
MY WORK:
Material Handling (6,000 + 8,000) x 3.84 = $53,760
Machine setups (20 + 20) x 330 = $13.200
Insertion of parts (6,000 + 8,000) x 30 = $420,000
Finishing (1,200 + 3,300) x 54 = $243,000
Total Overhead Cost $729,960
Standard: Deluxe:
Material Handling Cost 6,000 x 3.84 = $23,040 8,000 x 3.84 = $30,720
Machine Setup Cost 20 x 330 = $6,600 20 x 330 = $6,600
Insertion of Parts Cost 6,000 x 30 = $180,000 8,000 x 30 = $240,000
Finishing Cost 1,200 x 54 = $64,800 3,300 x 54 = $178,200
Total MOH Cost $274,440 $455,520
Homework hint: In E4-24A, under the traditional method of applying (allocating) overhead, the Deluxe unit looks like it makes us a gross profit of $65.99. But when we use Activity-Based Costing, it looks like we make only $64.98 in gross profit per Deluxe unit. (this was given by the professor)
E4-24A Continuation of E4-23A: Determine product profitability (Learning Objectives 2 & 3)
Refer to your answer in E4-23A. In addition to the manufacturing overhead costs, the following data are budgeted for the company’s Standard and Deluxe models for next year:
Standard Deluxe
Sales price per wheel………………. $420.00 $620.00
DM per wheel…………………….... $34.00 $47.00
DL per wheel………………………. $45.10 $52.50
Requirements
-
Compute the gross profit per wheel if managers rely on the ABC unit cost data computed in E4-23A.
-
Compute the gross profit per wheel if the managers rely on the plantwide allocation cost data.
-
Which product line is more profitable for Baltimore?
-
Why might the controller have expected ABC to pass the cost-benefit test? Were there any warning signs that Biltmore’s old direct-labor-based allocation system was broken?

Trending now
This is a popular solution!
Step by step
Solved in 3 steps with 2 images

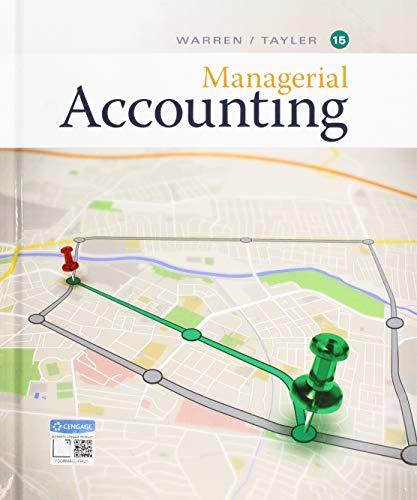
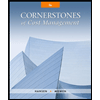
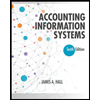
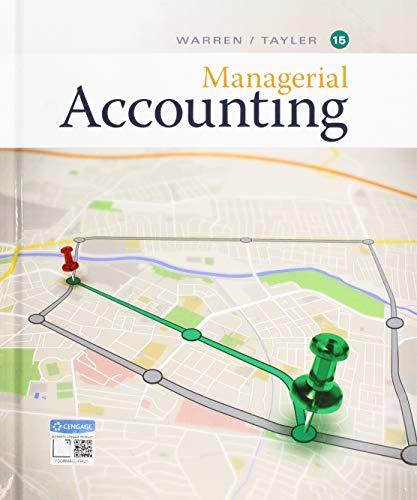
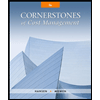
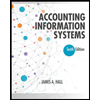