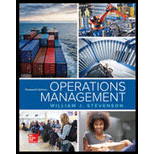
Concept explainers
a)
To determine: The number of machines of each type required to handle the demand and its capacity and the machine that would have lower total cost.
Introduction: Capacity planning is the process of planning the required production output based on the requirement or the demand that is predicted.
a)

Answer to Problem 11P
Explanation of Solution
Given information:
A company should decide whether to buy machine of type A, type B, or type C. The cost of type A machine is $40,000, cost of type B machine is $30,000, and the cost of type C machine is $80,000.
Annual demand and processing unit is given as follows for each product:
Product | Annual demand | Processing time per unit | ||
A | B | C | ||
1 | 16,000 | 3 | 4 | 2 |
2 | 12,000 | 4 | 4 | 3 |
3 | 6,000 | 5 | 6 | 4 |
4 | 30,000 | 2 | 2 | 1 |
Determine the number of machines of each type required and its capacity:
It is given that the machines will operate 60 minutes per hour, 10 hours per day and 250 days per year.
Determine the minutes available for all types of machine:
It is calculated by multiplying number of days per year, hours per day, and minutes per hour. Hence, the available minutes per year for machine type A, type B, and type C is 150,000 minutes per year.
Determine the processing requirement of product 1 using machine type A:
It is calculated by multiplying annual demand of product 1 and the processing time per unit on type A. Hence, the processing requirements of product 1 using machine type A is 48,000 minutes.
Determine the processing requirement of product 2 using machine type A:
It is calculated by multiplying annual demand of product 2 and the processing time per unit on type A. Hence, the processing requirements of product 2 using machine type A is 48,000 minutes.
Determine the processing requirement of product 3 using machine type A:
It is calculated by multiplying annual demand of product 3 and the processing time per unit on type A. Hence, the processing requirements of product 3 using machine type A is 30,000 minutes.
Determine the processing requirement of product 4 using machine type A:
It is calculated by multiplying annual demand of product 4 and the processing time per unit on type A. Hence, the processing requirements of product 4 using machine type A is 60,000 minutes.
Determine the total processing requirement using machine type A:
It is calculated by adding the processing requirement of all the products. Hence, the total processing requirement using machine type A is 186,000 minutes.
Determine the needed number of machine type A:
It is calculated by dividing the total processing requirement and available minutes for machine type A. Hence, the needed number of machine type A is 2 machines.
Determine the processing requirement of product 1 using machine type B:
It is calculated by multiplying annual demand of product 1 and the processing time per unit on type B. Hence, the processing requirements of product 1 using machine type B is 64,000 minutes.
Determine the processing requirement of product 2 using machine type B:
It is calculated by multiplying annual demand of product 2 and the processing time per unit on type B. Hence, the processing requirements of product 2 using machine type B is 48,000 minutes.
Determine the processing requirement of product 3 using machine type B:
It is calculated by multiplying annual demand of product 3 and the processing time per unit on type B. Hence, the processing requirements of product 3 using machine type B is 36,000 minutes.
Determine the processing requirement of product 4 using machine type B:
It is calculated by multiplying annual demand of product 4 and the processing time per unit on type B. Hence, the processing requirements of product 4 using machine type B is 60,000 minutes.
Determine the total processing requirement using machine type B:
It is calculated by adding the processing requirement of all the products. Hence, the total processing requirement using machine type B is 208,000 minutes.
Determine the needed number of machine type B:
It is calculated by dividing the total processing requirement and available minutes for machine type B. Hence, the needed number of machine type B is 2 machines.
Determine the processing requirement of product 1 using machine type C:
It is calculated by multiplying annual demand of product 1 and the processing time per unit on type B. Hence, the processing requirements of product 1 using machine type B is 32,000 minutes.
Determine the processing requirement of product 2 using machine type C:
It is calculated by multiplying annual demand of product 2 and the processing time per unit on type B. Hence, the processing requirements of product 2 using machine type B is 36,000 minutes.
Determine the processing requirement of product 3 using machine type C:
It is calculated by multiplying annual demand of product 3 and the processing time per unit on type B. Hence, the processing requirements of product 3 using machine type B is 24,000 minutes.
Determine the processing requirement of product 4 using machine type C:
It is calculated by multiplying annual demand of product 4 and the processing time per unit on type B. Hence, the processing requirements of product 4 using machine type B is 30,000 minutes.
Determine the total processing requirement using machine type C:
It is calculated by adding the processing requirement of all the products. Hence, the total processing requirement using machine type C is 122,000 minutes.
Determine the needed number of machine type C:
It is calculated by dividing the total processing requirement and available minutes for machine type C. Hence, the needed number of machine type C is 1 machine.
Determine the total cost considering purchase cost of machine type A:
It is calculated by multiplying number of machines and the cost of the machine. Hence, the total cost is $80,000.
Determine the total cost considering purchase cost of machine type B:
It is calculated by multiplying number of machines and the cost of the machine. Hence, the total cost is $60,000.
Determine the total cost considering purchase cost of machine type C:
It is calculated by multiplying number of machines and the cost of the machine. Hence, the total cost is $80,000.
Hence, Buying 2 of the B machines at a total cost of $60,000 have lower total cost.
b)
To determine: The machine that would have lower total cost considering operating cost.
Introduction: Capacity planning is the process of planning the required production output based on the requirement or the demand that is predicted.
b)

Answer to Problem 11P
Explanation of Solution
Given information:
A company should decide whether to buy machine of type A, type B, or type C. The cost of type A machine is $40,000, cost of type B machine is $30,000, and the cost of type C machine is $80,000.
Annual demand and processing unit is given as follows for each product:
Product | Annual demand | Processing time per unit | ||
A | B | C | ||
1 | 16,000 | 3 | 4 | 2 |
2 | 12,000 | 4 | 4 | 3 |
3 | 6,000 | 5 | 6 | 4 |
4 | 30,000 | 2 | 2 | 1 |
Operating cost for machine A is $10 per hour, operating cost for machine B is $11 per hour, and operating cost for machine C is $12 per hour.
Calculate the total cost considering both purchasing cost and operating cost for machine A:
It is calculated by adding the total cost considering purchasing cost and the operating cost which can be attained by multiplying operating cost per hour and the total processing hours.
Calculate the total cost considering both purchasing cost and operating cost for machine B:
It is calculated by adding the total cost considering purchasing cost and the operating cost which can be attained by multiplying operating cost per hour and the total processing hours.
Calculate the total cost considering both purchasing cost and operating cost for machine C:
It is calculated by adding the total cost considering purchasing cost and the operating cost which can be attained by multiplying operating cost per hour and the total processing hours.
Hence, buying two B machines would have lower total cost.
Want to see more full solutions like this?
Chapter 5 Solutions
Operations Management
- A manager must decide which type of machine to buy, A, B, or C. Machine costs (per individual machine) are as follows: Machine Cost $50,000 A B $40,000 C $70,000 Product forecasts and processing times on the machines are as follows: PROCCESSING TIME PER UNIT (minutes) Annual Product Demand 1 2 3 4 18,000 25,000 15,000 9,000 A 1 5 4 5 A B C B Click here for the Excel Data File 6531 Total processing time in minutes per machine: a. Assume that only purchasing costs are being considered. Compute the total processing time required for each machine type to meet demand, how many of each machine type would be needed, and the resulting total purchasing cost for each machine type. The machines will operate 8 hours a day, 220 days a year. (Enter total processing times as whole numbers. Round up machine quantities to the next higher whole number. Compute total purchasing costs using these rounded machine quantities. Enter the resulting total purchasing cost as a whole number.) C 2 1 2 6arrow_forwardA manager must decide which type of machine to buy, A, B, or C. Machine costs (per individual machine) are as follows: Machine Cost A B C Product forecasts and processing times on the machines are as follows: $80,000 $70,000 $40,000 Annual Product Demand 1 25,000 2 22,000 3 20,000 4 9,000 A B PROCCESSING TIME PER UNIT (minutes) A B C A 5 3 3 5 B 4 1 1 Click here for the Excel Data File Total processing time in minutes per machine: 296,000 196,000 6 a. Assume that only purchasing costs are being considered. Compute the total processing time required for each machine type to meet demand, how many of each machine type would be needed, and the resulting total purchasing cost for each machine type. The machines will operate 10 hours a day, 250 days a year. (Enter total processing times as whole numbers. Round up machine quantities to the next higher whole number. Compute total purchasing costs using these rounded machine quantities. Enter the resulting total purchasing cost as a whole…arrow_forwardThe next TWO questions refer to the following data. (This data may not be the same as in the ClearEyes Cataracts Clinic case.) Receptionist PSR Technician Staff Surgeon Cleaner Total annual minutes required per job title 29,450 353,268 212,882 119,944 51,820 Number workers by job title 1 4 3 1 1 Non-surgeons are available 115,200 minutes per year and surgeons are available 100,800 minutes per year. The average capacity utilization of the staff surgeon is: Group of answer choices 84.0 percent 91.5 percent 100.0 percent 104.1 percent 118.99 percentarrow_forward
- A manager must decide which type of machine to buy, A or B. Machine costs are as follows: Machine Cost A $110,000 40,000 Product forecasts and processing times on the machines are as follows:arrow_forwardA manager must decide how many machines of a certain type to purchase. Each machine can process 100 customers per day. One machine will result in a fixed cost of $2,000 per day, while two machines will result in a fixed cost of $3,800 per day. Variable costs will be $20 per customer, and revenue will be $45 per customer.a. Determine the break-even point for each range.b. If estimated demand is 90 to 120 customers per day, how many machines should be purchased?arrow_forwardDetermine the utilization and the efficiency for each of these situations:b. A furnace repair team that services an average of four furnaces a day if the design capacity issix furnaces a day and the effective capacity is five furnaces a dayarrow_forward
- A manager must decide how many machines of a certain type to purchase. Each machine can process 100 customers per day. One machine will result in a fixed cost of $2,100 per day, while two machines will result in a fixed cost of $3,900 per day. Variable costs will be $17 per customer, and revenue will be $45 per customer. a. Determine the break-even point for each range. (Round your answers to the next whole number.) One machine Two machines 4,500 b. If estimated demand is 90 to 120 customers per day, how many machines should be purchased?arrow_forwardWhat is CAPACITY REQUIREMENTS FORECASTING?arrow_forwardDetermine the utilization and the efficiency for each of these situations:a. A loan processing operation that processes an average of 7 loans per day. The operation has a design capacity of 10 loans per day and an effective capacity of 8 loans per day.b. A furnace repair team that services an average of four furnaces a day if the design capacity is six furnaces a day and the effective capacity is five furnaces a day.c. Would you say that systems that have higher efficiency ratios than other systems will always have higher utilization ratios than those other systems? Explain.arrow_forward
- J 1 ue K Beth Zion Hospital has received initial certification from the state of California to become a center for liver transplants. The hospital, however, must complete its first 10 transplants under great scrutiny and at no cost to the patients with the hospital picking the expenses. The cost per hour of surgery is estimated to be $5,000. The very first transplant, just completed, required 27 hours. On the basis of research at the hospital, Beth Zion estimates that it will have an 75% learning curve. Using Table E.3, estimate the time it will take to complete: a) the 10th transplant hours (round your response to two decimal places). Learning Curve Coefficients Unit Number (N) 10 Unit Time .385 75% Total Time 5.589 Unit Time .477 80% Total Time 6.315 Unit Time .583 85% Total Time 7.116 Xarrow_forwarda. what is the relationship between design capacity, system capacity, and actual output. b. how is a projected output within the boundaries of the design capacity and system capacity?arrow_forward1. A 32,000-seat baseball stadium is used 17 times for games, concerts, and graduation ceremonies. Each event averages five hours and assumes the stadium is full for each event. The stadium is available 365 days a year from 7 am to midnight. (Notice: the focus is stadium “seat” utilization). a. What is stadium (seat) utilization using Equation 7.1 (pg 146)? (Show your calculations) b. If in the above scenario, the utilization was 75% during the 17 events, but there were 2 additional events that garnered 100% utilization, would this be an increase or decrease in overall utilization from the result in “a”? (Show calculations) c. As an Operations Manager how would you improve utilization at the stadium? Provide at least three optional improvement plans with details. EQUATION 7.1 is : UTILIZATION (U) = Resources used / resources avaliable EQUATION 7.2 is: UTILIZATION (U) = Demand Rate / [Service Rate * Number of Servers]arrow_forward
- Practical Management ScienceOperations ManagementISBN:9781337406659Author:WINSTON, Wayne L.Publisher:Cengage,
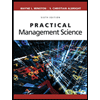