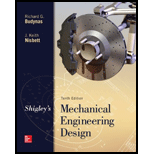
An M14 × 2 hex-head bolt with a nut is used to clamp together two 20-mm steel plates. Compare the results of finding the overall member stiffness by use of Eqs. (8-20), (8-22), and (8-23).
6-27 Using the modified Goodman criterion for infinite life, repeat Prob. 6-25 for each of the following loading conditions:
- (a) 0 kN to 28 kN
- (b) 12 kN to 28 kN
- (c) −28 kN to 12 kN
(a)

The yield factor of safety.
The fatigue factor of safety using Goodman criterion.
The number of cycle to failure.
Answer to Problem 27P
The yield factor of safety is
The fatigue factor of safety using Goodman criterion
The number of cycle to failure is
Explanation of Solution
Write the expression of endurance limit.
Here, endurance limit is
Write the expression for surface modification factor.
Here, surface modification factor is
Write the expression for endurance limit at critical location of a machine part in the geometry.
Here, the endurance limit at critical location is
Write the expression for fatigue stress concentration factor.
Here, the fatigue stress concentration is factor is
Write the expression for area of the steel bar at the hole or the minimum cross section area on which load is acting.
Here, width of the bar is
Write the expression for the maximum stress.
Here, the maximum force acting on the bar is
Write the expression for the minimum stress.
Here, the minimum force acting on the bar is
Write the expression for the nominal amplitude stress.
Here, the nominal amplitude stress is
Write the expression for the nominal midrange stress.
Here, the nominal amplitude stress for is
Write the expression for the amplitude component.
Here, the amplitude component is
Write the expression for the midrange component.
Here, the midrange component is
The Equation (XI) is valid when notch is present in the component.
Write the Expression for the yield factor of safety.
Here, the yield factor of safety is
Write the expression for the fatigue factor of safety using the modified Goodman criterion.
Write the expression for the completely reversed stress.
Here, the fatigue factor of safety using Goodman criterion is
Write the expression of number of cycle in case of completely reversed stress.
Here, the number of cycle are
Write the expression for the constant
Here, the strength fraction is
Write the expression for the constant
Conclusion:
Substitute
Refer to Table 6-2 “Parameter of Marin surface modification factor” to obtain the constant
Substitute
Refer to equation
Substitute
Refer to fig
Substitute
Substitute
Substitute
Substitute
Substitute
Substitute
Substitute
Substitute
Substitute
Thus, the yield factor of safety is
Substitute
Thus, the fatigue factor of safety using Goodman criterion is
Substitute
From fig-
Substitute
Substitute
Substitute
Thus, the number of cycle to failure is
(b)

The Yield factor of safety.
The fatigue factor of safety using Goodman criterion.
Answer to Problem 27P
The yield factor of safety is
The fatigue factor of safety is
Explanation of Solution
Write the expression of maximum stress.
Here, the maximum force acting on the bar is
Write the expression of minimum stress.
Here, the minimum force acting on the bar is
Write the expression of nominal amplitude stress.
Here, the nominal amplitude stress is
Write the expression of nominal midrange stress.
Here, the nominal amplitude stress for is
Write the expression of amplitude component.
Here, the amplitude component is
Write the expression of midrange component.
Here, the midrange component is
Write the Expression of yield factor of safety.
Here, the yield factor of safety is
Write the expression of fatigue factor of safety using the modified Goodman criterion.
Conclusion:
Substitute
Substitute
Substitute
Substitute
Substitute
Substitute
Substitute
Thus, the yield factor of safety is
Substitute
Thus, the fatigue factor of safety using Goodman criterion is
(c)

Yield factor of safety.
The fatigue factor of safety using Goodman criterion.
Number of cycle to failure.
Answer to Problem 27P
The yield factor of safety is
The fatigue factor of safety is
The number of cycle to failure is
Explanation of Solution
Write the expression of maximum stress.
Here, the maximum force acting on the bar is
Write the expression of minimum stress acting on the bar.
Here, the minimum force acting on the bar is
Write the expression of nominal amplitude stress.
Here the nominal amplitude stress is
Write the expression of nominal midrange stress.
Here, the nominal amplitude stress for is
Write the expression of amplitude component.
Here, the amplitude component is
Write the expression of midrange component.
Here, the midrange component is
Write the Expression of yield factor of safety.
Here the yield factor of safety is
Write the expression of fatigue factor of safety using the modified Goodman criterion.
Here the fatigue factor of safety is
Write the expression of number of cycle in case of completely reversed stress.
Here, the number of cycle are
Simplify the Equation (IX) for completely reversed stress and substitute
Write the expression of constant
Here, the strength fraction is
Write the expression of the constant
Conclusion:
Substitute
Substitute
Substitute
Substitute
Substitute
Substitute
Substitute
Thus, the yield factor of safety is
Substitute
Thus, the fatigue factor of safety is
From fig-
Substitute
Substitute
Substitute
Thus, the number of cycle to failure is
Want to see more full solutions like this?
Chapter 6 Solutions
Shigley's Mechanical Engineering Design (McGraw-Hill Series in Mechanical Engineering)
- Three round, copper alloy bars having the same length L but different shapes are shown, in the figure. The first bar has a diameter d over its entire length, the second has a diameter d over one-fifth of its length, and the third has a diameter d over one-fifteenth of its length. Elsewhere, the second and third bars have a diameter Id. All three bars are subjected to the same axial load P. Use the following numerical data: P = 1400 kN, L = 5m,d= 80 mm, E= 110 GPa. and v = 0.33. (a) Find the change in length of each bar. (b) Find the change in volume of each bar.arrow_forwardA polyethylene tube (length L) has a cap that when installed compresses a spring (with under-formed length L1) by an amount ?? = (L1 = L). Ignore deformations of the cap and base. Use the force at the base of the spring as the redundant. Use numerical properties given in the boxes. (a) What is the resulting Force-in the spring, Fk? (b) What is the resulting Force in the tube, Ftl (c) What is the filial length of the tube, Lf? (d) What temperature change ?T inside the tube will result in zero force in the springarrow_forwardThe inclined ladder AB supports a house painter (85 kg) at C and the weight iq = 40 K/m} of the ladder itself. Each ladder rail (t5= 4 mm) is supported by a shoe (ts= 5 mm) that is attached to the ladder rail by a bolt of diameter d = 8 mmarrow_forward
- 5-63 The figure shows a shaft mounted in bearings at A and D and having pulleys at B and C. The forces shown acting on the pulley surfaces represent the belt tensions. The shaft is to be made of AISI 1035 CD steel. Using a conservative failure theory with a design factor of 2, determine the minimum shaft diameter to avoid yielding. f-in R 300 Ibf 50 lbf 59 Ibf 392 lbf D Problem 5-63 C 6 in 8-in D. 8 in B 8 inarrow_forward6-25 The cold-drawn AISI 1040 steel bar shown in the figure reversed axial load fluctuating between 28 kN in compression to 28 kN in tension. Estimate the fatigue factor of safety based on achieving infinite life and the yielding factor of safety. If infinite life is not predicted, estimate the number of cycles to failure. 6-mm D. 25 mm Problem 6-25 10 mmarrow_forwardThe mounting arm shown in the figure below is to be made of machined AISI 1050 CD steel and is subjected to the aial force 120 An cyces repeatedy from tension to compression, and the completely reversitie cycd torsional moment of T25AN Assume the component is operating at room temperature of 0 and the material has sos refiablity factor. Aso asume K138 and-132 56 mm D r=3 mm %3D 50 mm D 1. Identity the critical location(s) of stress and show it clearly in a diagram 2 Identify cleary, all the components of stresses (at the critical point) that will be calculated (by drawing and clearly showing the XYZ axes) and show it in a matrix form Show which components of stresses will have a va zero or non-zero 3. Calculate the principar stresses and principal directions. Show the principal stresses dearty in a stress element with respect to original XYZ coordinate system 4. Clearly show the calculations for all the 6 Marin factors (Use only the formula sheet provided in the beginning of the test)…arrow_forward
- The figure shows a connection that employs three SAE grade 4 bolts. The tensile shear load on the joint is 4000 lbf. The members are bars of AISI 1020 HR steel. Assume the bolt threads do not extend into the joint. Find the factor of safety for each possible mode of failure. (Refer example problem 8.6 on pg. 445). in ∞ in 100 in 1 in in Đ 1in -2 in in-20 UNC 5 5 in inarrow_forwardAgui - 4550/2 =2276 two plates each with thickness t - 16 mm are bolted together with 6-222 mndia. bolts firming alap Joint Bolt spacing are follows St- $40mm S2 - 80mm, S3=150mm effective bolt hole dia. is 25mm A36 is used. Compute the allowable tensile Strength P t = 16 mm &t 52 747₁ 0 O O 40 60 80 40 +=16mm S-400 $3-100 S2-40 7 @ 4umm Parrow_forward8-69 The bolted connection shown in the figure is subjected to a tensile shear load of 90 kN. The bolts are ISO class 5.8 and the material is cold- drawn AISI 1015 steel. Find the factor of safety of the connection for all possible modes of failure. Tarrow_forward
- 8-68 Engineering Design + 40 1 plem 8-68 70 millimeters. 40 A bolted lap joint using ISO class 5.8 bolts and members made of cold-drawn SAE 1040 steel is shown in the figure. Assume the bolt threads do not extend into the joint. Find the tensile shear load F that can be applied to this connection to provide a minimum factor of safety of 2.5 for the fol- lowing failure modes: shear of bolts, bearing on bolts, bearing on members, and tension of members. 20 M20x2.5 20arrow_forward7-5 A rotating step shaft is loaded as shown, where the forces FA and F3 are constant at 600 lbf and 300 lbf. respectively, and the torque T alternates from 0 to 1800 lbf - in. The shaft is to be considered simply supported at points O and C, and is made of AISI 1045 CD steel with a fully corrected endurance limit of S₂ = 40 kpsi. Let Kf = 2.1 and K = 1.7. For a design factor of 2.5 determine the minimal acceptable diameter of section BC using the (a) DE-Gerber criterion. (b) DE-Goodman criterion. n 6 in FA = 600 lbf 6 in FB = 300 lbf 6 in T, n Page 413arrow_forwardThe bolted connection shown in the figure is subjected to a tensile shear load of 100 kN. The bolts are ISO class 5.8 and the material is cold-drawn AISI 1040 steel. Find the factor of safety of the connection for all possible modes of failure. 35 - 35 15 M20 x 2.5 35 35 - 20arrow_forward
- Mechanics of Materials (MindTap Course List)Mechanical EngineeringISBN:9781337093347Author:Barry J. Goodno, James M. GerePublisher:Cengage Learning
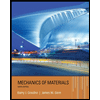