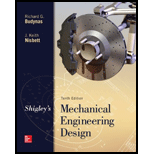
Concept explainers
For the sake of perspective it is always useful to look at the matter of scale. Double all dimensions in Prob. 9-18 and find the allowable load. By what factor has it increased? First make a guess, then carry out the computation. Would you expect the same ratio if the load had been variable?

The allowable load.
The factor at which the allowable load is increased.
Answer to Problem 53P
The allowable load is
The factor at which the allowable load is increased is
Explanation of Solution
Write the expression for throat area.
Here, the weld thickness is
Write the expression for primary shear stress due to shear force.
Here, the shear force is
Write the expression for unit second polar moment of area.
Here, width of weld is
Write the expression for second polar moment of area.
Write the expression for length of centroid from force.
Here, distance of unfix bar is
Write the expression for bending moment.
Here force acting on the bar is
Write the expression for radius of torsion in.
Write the expression for radius of torsion in
Write the expression for secondary shear in
Write the expression for secondary shear in
Write the expression for net shear stress.
Write the expression for throat area.
Here, the weld thickness is
Write the expression for primary shear stress due to shear force.
Here, the shear force is
Write the expression for unit second polar moment of area.
Here, width of weld is
Write the expression for second polar moment of area.
Write the expression for length of centroid from force.
Here, distance of unfix bar is
Write the expression for bending moment.
Here force acting on the bar is
Write the expression for radius of torsion in.
Write the expression for radius of torsion in
Write the expression for secondary shear in
Write the expression for secondary shear in
Write the expression for net shear stress.
Write the expression for increased factor.
Conclusion:
Substitute
Substitute
Substitute
Substitute
Substitute
Substitute
Substitute
Substitute
Substitute
Substitute
Substitute
Substitute
Substitute
Substitute
Substitute
Substitute
Substitute
Substitute
Substitute
Substitute
Substitute
Substitute
Thus, the allowable load is
Substitute
Thus, the factor at which the allowable load is increased is
Want to see more full solutions like this?
Chapter 9 Solutions
Shigley's Mechanical Engineering Design (McGraw-Hill Series in Mechanical Engineering)
- You are given a square rod of 6061-T6 aluminum (cross-section = 4mm X 4mm, length = 2.3m). The material has a Young’s modulus of 72 GPa. If a tensile load of 3 kN is applied parallel to the 2.3m dimension, what is the change in length of the rod?arrow_forwardFor the following problem please show intermediate steps including free body diagrams, equation used, problem setup etc. so that your approach can be followed. Finally please put the answer in a box with the appropriate unit.arrow_forwardSolve the preceding problem if the thickness of the steel plate is. t = 12 mm. the gage readings are x = 530 × 10-6 (elongation) and y = -210 -× l0-6 (shortening), the modulus is E = 200 GPa, and Poisson’s ratio is v = 0.30.arrow_forward
- A solid truncated cone is subject to an axial force P as shown. The exact elongation is d = PL/ (2pc²E). Replace the cone by n equal thickness circular cylinders and derive the expression as a function of n, P, L, C, E. draw a graph showing variation in elongation d with respect to n values. Take n from 1 to 100. Given that the P = 1 kip, L = 12 inch, C= 4 inch, E = 30x10° psi. B 2carrow_forwardasaparrow_forwardConsider the material Al-$456 It has the following physical ploperties Syleld = 230mPA %3D s-72GPA (modulos elasticity) Oultimate=315 mPA G- 28GPA Cmad vlus rigidity) Tuield =130 mPA Joltimate=185 mPA A Calculate Poisson's ratio B) If we have a following dimensions And Forces 3-0 block of Al-5456 with the Ex =800N X= Bcm Fy=1000N ) Is Our block Safes (consider only plane stes) Dset up the 3 eqetions to find the strains (Ex Ey E2) in each directian E Solve the 3exuations to find the Einal dimensions of our blockarrow_forward
- The plate of the figure is subjected to a bending moment with irregular cycles, which are repeated. In the graphic one of this cycles is represented in terms of stress which appears in each section whose height is h. The piece is made of ductile steel. Determine the number of repetitions of the sequence which the piece can resist before the failure takes place due to fatigue considering a reliability of 95 %. Data: Sult = 1.000 MPa Syp 3D800 Mра thickness e = 4 mm H = 10 cm h = 5 cm r=1 cm ka = 0,72 kp = 0,95 S(MPa) M 400 h 300 200 100 W -100 -200arrow_forwardcylindrical pressure vessel has inside diameter d_{o} = 500 mm and inside diameter di=490 mm.if it i made of carbon steel SAE 1040 OQT1300, find the maximum allowable internal pressure if the safety factor against yielding is not to be less than 4. Neglect the external pressure and assume that the longitudinal stresses are taken by the vessel itself. a) Solve using the MSST. b) Solve using the DET. See Appendix 3 for material properties.arrow_forwardThe stress-strain diagram for a steel alloy having an original diameter of 0.80 in and a gage length of 10 in. is shown in the figure below. (Figure 1) Figure (ks) 70 40 30 40 30 20 10 0 004 00 - 612 636 630 6.34 0.38 BLS GURE LUNGS GORD 1 of 1 (in/in) X Incorrect; Try Again; 2 attempts remaining Part B Determine the load on the specimen that causes yielding Express your answer to three significant figures and include appropriate units. Py = 74 Submit kips Previous Answers Request Answer ?arrow_forward
- pls find box ur answer Determine the value of the von Mises stress at point A. The von Mises stress at point A is This problem illustrates that the factor of safety for a machine element depends on the particular point selected for analysis. Here you are to compute factors of safety, based upon the distortion-energy theory, for stress elements at A and B of the member shown in the figure. This bar is made of AISI 1006 cold- drawn steel and is loaded by the forces F= 0.55 kN, P = 4 kN, and T = 25 N-m. Given: Sy= 280 MPa. 5 15-mm D. 100 mm- MPa.arrow_forwardWrite a short explanation for the following terms: 1. Strain 2. Young's Modulus of Elasticity 3. Design Limit Load & Design Ultimate load 4. Safe-life 5. Fail-safe structure 6. Fatigue 7. Loads on fuselagearrow_forwardCalculate the elustic limit of the plate 10 plate 8X0 - S00 pounds of load material 6061 Aluminum - Determine whattypeof stress is acting at this point -calculate the magnitude of this stressarrow_forward
- Mechanics of Materials (MindTap Course List)Mechanical EngineeringISBN:9781337093347Author:Barry J. Goodno, James M. GerePublisher:Cengage Learning
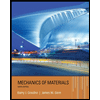